This standard is a reaffirmation of ANSI/ASQC Z1.4-2003, “ Sampling Procedures and Tables for Inspection by Attributes.” Suggestions for improvement of this standard are welcomed. Send your comments to the sponsor, ASQ Standards, 600 North Plankinton Avenue, Milwaukee, WI 53203. Download ANSI tables in PDF format here: TABLE I – Sample Size Code Letters. TABLE II – A – Simple sampling plan for normal inspections (Master Table) TABLE III – A – Double sampling plan for normal inspections (Master Table) The ANSI Z1.4 2003 standard is also known under the following names: ISO 2859, NF06-022, BS 6001.
- adsense:block:AdSense1 This application designs a sampling plan for variables, according to the ANSI/ASQ Z1.9 tables, for a given lot size and AQL. It also calculates the estimated percent defectives in a lot, given the known or estimated variability. For the MIL-STD-414 tables click here. More about acceptance sampling plans. Enter your process parameters: Variability.
- ASQ/ANSI Z1.4–2003 (R2018) SAMPLING PROCEDURES AND TABLES FOR INSPECTION BY ATTRIBUTES This standard is a reaffirmation of ANSI/ASQ Z1.4–2003 (R2013) This is a preview of 'ANSI/ASQ Z1.4 2003 (.' Click here to purchase the full version from the ANSI store.
ASQ Z1.4-2008 and Z1.9-2008 SET ASQ Z1.4-2008 and Z1.9-2008 SET Sampling Procedures and Tables for Inspection by Attributes (Z1.4-2008) and Sampling Procedures and Tables for Inspection by Variables for Percent Nonconforming (Z1.9-2008) SET American Society for Quality / 2008 / 213 pages. ANSI/ASQ Z1.13-1999. Convert Pdf To Txt Files In Ansi Code Codes and Scripts Downloads Free. Aostsoft PDF to Office Document Converter is a competent and utility program specially used to batch convert PDF to Word(. How to Manipulate Files in ASP.
This standard is a revision of ANSI/ASQC Z,. “Sampling Procedures and Tables for Inspection by. Attributes.” Beyond editorial refinements, only the. Know the switching rules for ANSI/ASQ Z Categorize the various sampling plan systems in terms of lot-by-lot, continuous production, attributes or variables. ANSI/ASQ Z Sampling Procedures and Tables for Inspection By. Attributes The FDA recognizes ANSI/ASQ Z as a General consensus standard.
Ansi Asq Z1.4 Table Free
Author: | Zuzuru Vulrajas |
Country: | Congo |
Language: | English (Spanish) |
Genre: | Science |
Published (Last): | 4 July 2011 |
Pages: | 469 |
PDF File Size: | 20.23 Mb |
ePub File Size: | 2.44 Mb |
ISBN: | 486-9-21793-340-5 |
Downloads: | 48279 |
Price: | Free* [*Free Regsitration Required] |
Uploader: | Mazubei |
On the other hand, if the lot sampling is to detect lots with specific faults, isolated to a specific specification then the defect types would be considered separately. I wish there was a simple answer. These rules are designed to encourage suppliers to have process averages consistently better than the AQL. If the inspection ansii requires lot sampling, then all of the basic lot sampling guidelines apply. Acceptance Sampling With Rectification When Inspection Errors Are Present, Journal of Quality Technology In this paper the authors consider the problem anwi estimating the number of nonconformances azqc in outgoing lots after acceptance sampling with rectification when inspection errors can occur.
They show the average sample size for scheme performance when using single sampling. Use corresponding double sampling plan.
Ansi Asq Z1.4 Table Free Form
The standard 1z.4-2008 not intended as a procedure for estimating lot quality or for segregating lots. Table X-D—Tables for sample size code letter: It is expected that the product quality level will be less than the AQL to avoid excessive non-accepted lots. If the document is revised or amended, you will be notified by email.
Normal inspection will be used at the start of inspection unless otherwise directed by the responsible authority.
ASQC Q contains sampling plans that have been calculated on this basis and therefore provide a more accurate set of tables for these situations. We want to ensure that we are receiving clean containers to package our products.
AOQL values are given in Table V-A for each of the single sampling plans for normal inspection and in Table V-B for each of the single sampling plans for tightened inspections. The number of nonconformities per hundred units of any given quantity of units of product is one hundred times the number of nonconformities contained therein one or more nonconformities being possible in any unit of product divided by the total number of units of product, i.
Is this instance, more than ten lots or batches may be used for the calculation, provided that the lots or batches used are the most recent ones in sequence, that they have all been on normal inspection, and that none has been rejected while on original inspection. Components and raw materials.
The number of sample units inspected shall be equal to the sample size given by the plan. If sample size equals or exceeds lot or batch size, do percent inspection. However, Inspection Level I may be speci?
Subscription pricing is determined by: The sample size to be used is given by the new code letter, not by the original letter. Purchasers of American National Standards may receive current information on all standards by calling or writing the American National Standards Institute. Three types of sampling plans: As necessary, the supplier shall provide adequate and suitable storage space for each lot or batch, equipment needed for proper identi?
This standard is intended to be used as a system employing tightened, normal, and reduced inspection on a continuing series of lots to achieve consumer protection while assuring the producer that acceptance will occur most of the time if quality is better than the AQL. If you use one of the special sampling plans based on the cost of the test, it is helpful to calculate the actual AQL and Limiting Quality LQ using the following formulas.
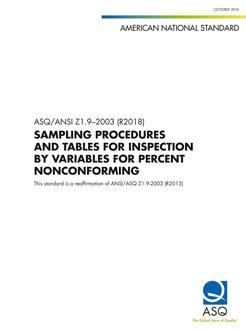
Once that confidence is restored, then you go back to what you inspected originally. Ideally, a very fast, effective and non-destructive inspection method is preferred over a slow, error prone, and destructive approach.
Z1.4:2008 inspection levels
When no sampling plan is available asqqc a given combination of Z1.4-200 and code letter, the tables direct the user to a different letter. Skip to content Z1.4-208 Original inspection is the? American National Standards are subject to periodic review and users are cautioned to obtain the latest editions. My concern with the current method is that you may have a lot of extra paperwork to account for everyone for a certain time.
My second question is if I have a batch that passes acceptance sampling but at a subsequent downstream process a defect being inspected for by the upstream acceptance sampling inspection is found how do I determine if the lot is acceptable?
Zero defect sampling is an alternative method to the obsolete Mil Std E sampling scheme previously used to accept or reject products, and the remaining ANSI Z1.
Ssqc the use of this standard it is helpful to distinguish between: When agreed upon by responsible authority for both parties to the inspection, that is, the supplier and the end item customer, the requirements of 8. Once on tightened inspection, unless corrective action is taken to improve product quality, it is very likely that the rule requiring discontinuance of sampling inspection will be invoked.
ANSI/ASQ Z1.4–2003 (R2013): Sampling Procedures and Tables for Inspection by Attributes

Ansi Asq Z1 4 2013 Pdf
The term scheme performance is used here in a very restrictive sense. Less discrimination means that z14-2008 actual Acceptable Quality Level AQL on the table underestimates the true AQL, as the sample size has been reduced from the table-suggested sample size i.
The operating characteristics and other measures of a plan so chosen must be assessed individually for that plan from the tables provided. The responsible authority shall determine whether normal or tightened inspection shall be used on reinspection and whether reinspection shall include all types or classes of nonconformities or only snsi particular types or classes of nonconformities which caused initial rejection.
Z inspection levels –
Ansi Asq Z1 4 2008
Please first log in with a verified email before subscribing to alerts. To me, it feels like the first step should be to determine the AQL. Need more than one copy?
The ideal method of calculating the sample size and risk is by use of the hypergeometric probability function.
AOQL will be slightly higher when the limit numbers for reduced inspection are not used under Option 8. When several types of plans are available for a given AQL and code letter, any one may be used.
Most Related
By Crystal Ge
Many importers don’t bother to learn about AQL sampling for product inspection because they think the AQL table is too technical. The numbers, letters and terminology surrounding the ANSI ASQ Z1.4 standard table, common for most inspections, can seem a little intimidating at first. So these importers often leave the details of understanding acceptable quality levels (AQLs) to QC professionals.
But the truth is that anyone can easily understand and apply the table, not just QC professionals. And as an importer, familiarity with the different parts of the table and how they work together will help you to better monitor and improve the quality of your products before they leave the factory (related:The Importer’s Guide to Managing Product Quality with AQL [eBook]).
There are five main parts of the single-sampling AQL table: lot sizes, inspection levels, sample size code letters and acceptable quality levels. Let’s explore these and see how they interact with one another.
1. Lot size
On the far left of the first side of the chart you’ll see a section for “lot size”, referring to your total order quantity. Lot size is your starting point for using the table, represented by a series of ranges of order quantities expressed in units. You’ll choose the lot size range containing your total order quantity. For instance, let’s say you have an order quantity of 300 tablet PCs. You’d use the lot size range of 280 – 500 units.
2. Inspection level
The first part of the table is further divided into columns between two categories, “general inspection levels” and “special inspection levels”, each class with a different application. The inspection level you choose is a critical determinant of the scope of your product inspection. So it’s important you consider your product quality standards, customer expectations and time and budget constraints when choosing.
General inspection levels
Inspectors use general inspection levels for procedures that are intended to be performed on their main sample size which includes all SKUs in the order. This typically means a visual inspection of the product to look for quality defects and nonconformances, as well as conducting any on-site tests and checks that cover your main sample. Some examples related to tablet PCs are checking assembly, retail packaging contents and packing assortment. Since these checks can be done relatively quickly, it makes sense to include them in “general” inspection.
General inspection levels are divided in three smaller columns—“GI”, “GII” and “GIII”—each with its own set of sample size code letters corresponding to specific lot size ranges. Among these three levels, GI is associated with the smallest sample size. Considered the “budget option, GI may be best if you’re pressed for time or money and don’t require a particularly thorough inspection of an order.
GIII is the tightest standard and requires the inspection of a larger sample size, providing a more comprehensive assessment of an order’s overall quality. The disadvantage of GIII is that the larger sample size tends to require more time to inspect, which makes it the most expensive option. GII is the moderate option and is the most common inspection level for inspecting consumer goods.
Special inspection levels
You’ll typically use special inspection levels for special product tests that should only be conducted on a relatively small sample of units. Smaller sample sizes are usually needed because such tests either:
- Are destructive to the product
- Are expensive or tedious to perform, or
- Tend to yield similar results across all units in the order
An example of a product test that can be destructive and applies to most products, including tablet PCs, is the carton drop test. Other tests, like the battery recharging test and port function & insertion/removal test, are time consuming. And it’s not necessary to check printing adhesion on a large number of tablets, since the process for applying the print almost never varies between units of the same SKU.
Special inspection levels are divided in four: “S1”, “S2”, “S3” and “S4”. As with general inspection levels, S1 offers the smallest sample size and S4 offers the largest. Your decision to use special inspection levels will likely depend on what is applicable to your product type. Just be sure to include your requirement in a detailed QC checklist for your supplier and inspection team (related: How to Address On-Site Product Testing in a QC Checklist).
3. Sample size and code letters
After determining your lot size and inspection level, you’re ready to determine your sample size. Sample sizes are represented by code letters on the first part of the table. By following the row of your lot size to your chosen inspection level, you’ll see a corresponding code letter listed. The second part of the AQL chart lists the sample size, or the number of units to pull for inspection, next to the corresponding code letter.
Contrary to popular belief, lot size actually has little influence on the chosen sample size. That’s because, if you choose a relatively low tolerance for defects (AQL), you can have a small lot size but still require a larger sample size than that lot size dictates. The lower your tolerance for defects, the more units you’ll need to inspect to reasonably predict the average quality of the total order. If the appropriate sample size equals or exceeds your lot size, you’ll inspect 100 percent of the order.
Whereas for large lot sizes with higher AQLs, a larger sample size is often redundant. That is, you can get the same confidence in results from inspecting a smaller sample size, which will be less time consuming and less expensive.

On the second part of the AQL chart, under each of the acceptable quality levels, there are arrows pointing up or down for certain sample sizes. These arrows indicate where the selected sample size is inadequate or redundant, as explained above. In these cases, follow the arrows to the appropriate sample size and use this sample size for your inspection.
Let’s say your chosen inspection level for your order of 300 tablet PCs is GII. From the first part of the AQL chart, we can see the corresponding sample size code letter is “H”. But if you’re using an AQL of 0.65, you’ll need to use a sample size of 80 units, instead of the 50 unit sample size corresponding to H, as shown by the downward arrow.
4. Acceptable quality levels (AQL)
Sometimes called “acceptable quality limits”, AQLs range from 0 to 15 percent or more, with 0 representing the lowest tolerance for defects. Importers’ tolerance for “minor” defects tends to be higher than that for “major” and “critical” defects. So they usually choose a different AQL for each of these classes of product defects. For consumer goods, QC professionals typically recommend AQLs of 0, 2.5 and 4 percent for critical, major and minor defects, respectively (related: 3 Types of Quality Defects in Different Products).
Choosing an AQL isn’t always as simple as adopting the one that similar importers are using. What works for one importer might not work for another to verify that orders are meeting customer expectations. To ensure you can choose the best AQL for your circumstances, there are a number of factors to consider, including:
- What quality level your supplier considers reasonable and has agreed to meet
- Your inspection budget (lower AQLs typically require larger sample sizes and more time)
- Your exit-factory date
- The value of the goods in question (more expensive products tend to warrant lower AQLs)
Although you might select what you perceive as a reasonable AQL to apply, that doesn’t mean a factory will feel the same way. Agreeing upon standards early is crucial when it comes to QC inspection. The factory may try to dispute the results of an inspection if there’s no prior agreement on an appropriate AQL (related: How AQL Sampling Affects Your Product Inspection Results).

5. Acceptance points and rejection points
Your chosen AQL for each type of defect will determine a corresponding acceptance point and rejection point. The acceptance point indicates the maximum number of defects you’ll accept in the order, while the rejection point indicates the minimum number of defects needed to reject the order. For example, an AQL of 0 for critical defects has a rejection point of 1 defect. This means that if inspectors find even one critical defect, the inspection result will be “fail”.
Acceptance and rejection points increase as your tolerance for a defect increases, respective to sample size. If you choose an AQL of 1 with a sample size of 125 units (denoted by the code letter “K” on the AQL chart), your acceptance point is 3 defects and your rejection point is 4 defects. But, perhaps you decide your tolerance for this defect is actually much higher and an AQL of 4 is more appropriate. The corresponding acceptance and rejection points will be much higher as well, at 10 and 11 defects, respectively.
Conclusion
Behind all of the numbers and letters on the AQL chart is statistical reasoning that ensures the sample size you inspect provides a reasonable representation of your order’s overall quality. And one positive aspect of AQL is that you don’t have to understand technical details and complex formulas to be able to use it for sampling and inspection.
But completely understanding the anatomy of the table will help you prevent mistakes when using AQL for inspection. Using AQL properly also helps reduce your chances of unwittingly shipping goods that don’t meet your quality standards (related:How Importers use the AQL Table for Product Inspection). And if you want to find out your required sample size and acceptance and rejection point quickly, you can always use our AQL calculator.
Ansi Z1.4 Table
Crystal Ge is a Client Manager at InTouch Manufacturing Services, a QC firm that performs product inspections and factory audits in Asia for clients in the US, EU and Australia.
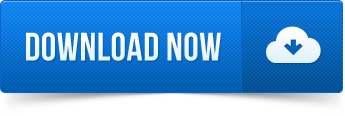
Comments are closed.